Getting to the point of applying your color matched gelcoat is one of the last steps in finishing off your repair(s). In the video I mentioned that there were 2 common ways to do this; spraying or brushing..
While brushing the gelcoat has it’s advantages, it isn’t always the best approach. For small patches such as chips, dings, scratches and small repairs I believe that it is the most efficient both in prep time and application. However in situations where the repair spot is much larger than what is shown in the video, spraying is definitely the way to go.
Looking at this option a little further, lets go over some of the options for equipment. The first thing that will be needed regardless of the type of spray gun used (we’ll cover this in a bit), is a large compressor. At a minimum a 3hp unit will be needed with a 60 gallon tank. This will provide most of the air needed with brief pauses to let the pressure build back up. Ideally, a 5hp unit will provide everything that you’ll require and then some; the compressor will be able to ‘catch up’ with the demand and occasionally turn off. 3HP units will run constantly and can tend to get a little ‘warm’ 🙂 However, they do work! It’s what I have and so far (knock on wood) haven’t run into any issues.
With that part of the equation in place, now it’s time to talk about guns. Keeping in mind that gelcoat is a resin that has a relatively short working time before it starts to set up (normally 10 min depending on the % catalyst used) I like to use guns that can be broken down quickly. For the most part, this boils down to gravity style guns and cup guns (aka dump guns).
Pictured below is an example of a cup gun. These types of units are an ‘industry standard’ for higher volume application needs. This particular unit is the ES-100, I believe the newer model is the ES-120.
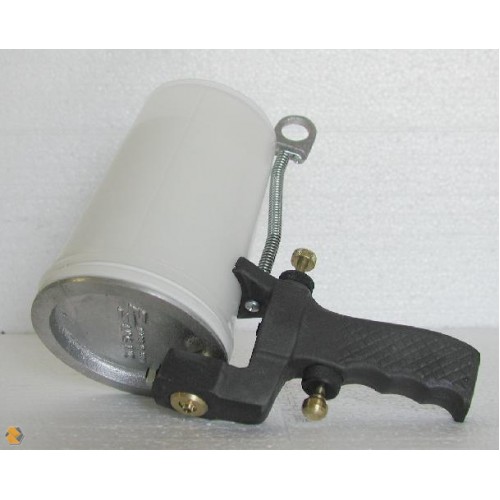
Advantages of this type of gun are:
– The gelcoat can be applied with very little to no thinning
– Simple design which allows quick break down for cleaning
– It’s able to “dump” a lot of material quickly and efficiently
In my opinion, the most attractive benefit of this is that the gelcoat does not require thinning. Whenever a material is thinned it displaces it’s properties. By this I am referring to UV-absorbers and pigments / color. A material that has been reduced will require a thicker film for the same level of protection versus un-thinned applications. Also, when spraying laminating gelcoat (no wax additive), use of PVA will be required to achieve a full cure.
This being said, nothing is perfect. The downside of spraying thick material is that it will not give as smooth of a finish out of the gun, requiring more wetsanding to get the desired appearance.
The other style of gun mentioned is a typical gravity fed gun such as that shown here:

Use of this type of sprayer will require thinning the gelcoat to get proper atomization. These units are typically less expensive and can be viewed as semi-disposable. If the gelcoat happens to set up in the gun before cleaning, they can be replaced for $15-$20. Note: These cheap units will NOT provide a good finish with paints! A good paint gun can easily cost $500 or more 🙂
When we start to look at thinners (or more accurately gelcoat additives) there are two brands that I’ve used with good results. Duratec Clear High Gloss Additive, and Patch-Aid. These are both what are considered to be ‘reactive thinners’ rather than evaporative thinners. The difference being that reactive thinners actually become part of the gelcoat and cure together as one film. Evaporative thinners are as they sound, the solvent evaporates from the gelcoat leaving behind mostly straight gelcoat. Styrene and acetone would be examples of evaporative thinners. A lot of Pro’s use these types of thinners, however in my opinion they are more toxic to work with and not as ‘user friendly’. Personally I like to use additives such as the Duratec or Patch-aid.
Use of these additives does change the way that the overall mix needs to be catalyzed. Normal gelcoat should be catalyzed at around 1% – 1.25% Mek-P. When using these additives, the overall mix needs to be catalyzed at 2% or higher (it will be stated on the product container). Also, when these products are mixed in, no PVA is required to achieve a full cure.. That’s one of the benefits of these additives, and for this feature alone, I feel it makes them a very user friendly way to spray gelcoat for the DIY.. Also, because the material being sprayed has better atomization, it will provide a smoother finish out of the gun, requiring less wetsanding 🙂
HERE is a mixing chart showing the ratio’s for the various % of Mek-P courtesy of one of my local vendors, Express Composites.